Noticias
La electrónica embebida en sistemas de control e instrumentación industrial está trayendo enormes beneficios a las áreas de mantenimiento. Concretamente en la lubricación, la dosificación de grasas y aceites en dispositivos no solo asegura la confiabilidad de los equipos, sino que evita daños en componentes que, en ocasiones, pueden ser de carácter crítico para la operación.
La corrosión es el principal enemigo de cualquier mecanismo, sobre todo cuando las condiciones de humedad, temperatura o exposición a polvo o ambientes hostiles en general son extremas. Los técnicos en mantenimiento y lubricación tienen una significativa responsabilidad de realizar la tarea permanente de revisión y aplicación de aceites o grasas que eviten las situaciones de fricción o desgaste que puedan causar daños a los equipos.
Lea también: "4 retos de la manufactura moderna"
Esto siempre da margen para los errores humanos, como pueden ser desde la desatención o mala programación de la supervisión hasta la aplicación equivocada de algún lubricante. Esto provoca que componentes como engranajes, cojinetes o rodamientos se sometan a un estrés excesivo y acelerado.
La aplicación incorrecta o mal programada de lubricante puede generar estrés excesivo, fricción y desgaste en los
componentes.
Este tipo de deficiencias o, incluso, descuidos en la lubricación causa daños multimillonarios cada año en las empresas. Estudios de NACE, un organismo que aglomera a los expertos en corrosión, establecida en 1943 en la ciudad de Houston, Texas, indican que la corrosión cuesta a las empresas alrededor de 2.5 mil millones de dólares en el mundo, cálculo que no incluye aspectos medioambientales ni de seguridad en el trabajo.
Debido al enorme número de puntos de lubricación existentes en las instalaciones industriales, la automatización ha ido ganando cada vez más terreno, pues esos aseguran la dosificación permanente de un componente en función de sus necesidades y características particulares.
Hoy en día existen sistemas de lubricación automáticos que permiten programar su aplicación hasta por 24 meses.
Algunos de estos equipos pueden programarse por hasta 24 meses, proveyendo de aceite de manera permanente con algoritmos que les permiten compensar pérdidas de presión para asegurar que la dosis siempre sea homogénea. Estos equipos se pueden instalar con mangueras de conexión y funcionar con baterías, o bien, con corriente directa conectado, por ejemplo de un PLC.
Industrias como las de alimentos y bebidas, petroquímica o farmacéutica se mueven cada vez más en esta dirección. Es innegable que estas tecnologías son cada vez más visibles para los departamentos de mantenimiento, en gran medida debido a la digitalización y el movimiento tecnológico auspiciado por el concepto alemán de Industria 4.0, que se acerca más a un modelo de conectividad entre los equipos e instrumentos, no obstante, esto no es tan acelerado en todas las industrias.
Lo anterior tiene un beneficio adicional relacionado con el monitoreo y seguimiento de las tareas de lubricación. La naturaleza digital de los equipos automáticos de lubricación asegura la generación de información que pueden transmitirse en tiempo real y, en algunos casos, ser ajustados remotamente.
Lea también: "Las historias que cuentan los datos"
También, esta información puede concentrarse en repositorios de bases de datos que luego puedan ser tomados por sistemas de analítica avanzada, que en suma con la información de los equipos y componentes en funcionamiento, potencializa la toma estratégica de decisiones.
Se calcula que el uso de instrumentos de lubricación automática tiene un retorno de inversión menor a un año, pero el impacto de sus beneficios es enorme debido a que pueden evitar daños de un valor muy elevado o bien, reducen el riesgo de afectaciones al personal, sobre todo en aquellos ambientes hostiles o incluso peligrosos.
Existen varios tipos de sistemas, como los paralelos de una sola línea, los de doble línea y el progresivo de una sola línea; cada uno tiene diferencias en cuanto a instalación o a funcionamiento y capacidad de configuración y dosificación. Conocer bien las necesidades de lubricación de cada punto, al final es lo más importante y requiere de un alto grado de especialización en tribología por parte del personal de mantenimiento, pues de hacerse bien la instalación, se obtiene un beneficio total de cada dispositivo.
La utilización de sistemas de lubricación automática alargan la vida útil de los equipos de proceso y de la maquinaria, aseguran la confiabilidad de los equipos y de la operación, reducen los paros no programados y pueden brindar (en función de las características de cada instrumento) información en tiempo real del proceso, lo que en consecuencia mejora el conocimiento de los equipos y aporta un valor significativo al valor estratégico del mantenimiento y la lubricación en las estrategias de producción.
Por ello, este tipo de soluciones estarán presentes en Expo Manufactura 2023, uno de los eventos industriales más importantes a nivel nacional, que reúne a empresas líderes para presentar innovaciones y tecnología que dan solución a las diferentes necesidades del sector, como los instrumentos de lubricación automática.
La edición número 27 de Expo Manufactura se llevará a cabo del 7 al 9 de febrero del siguiente año en Cintermex, en Monterrey, Nuevo León.
Otras noticias de interés
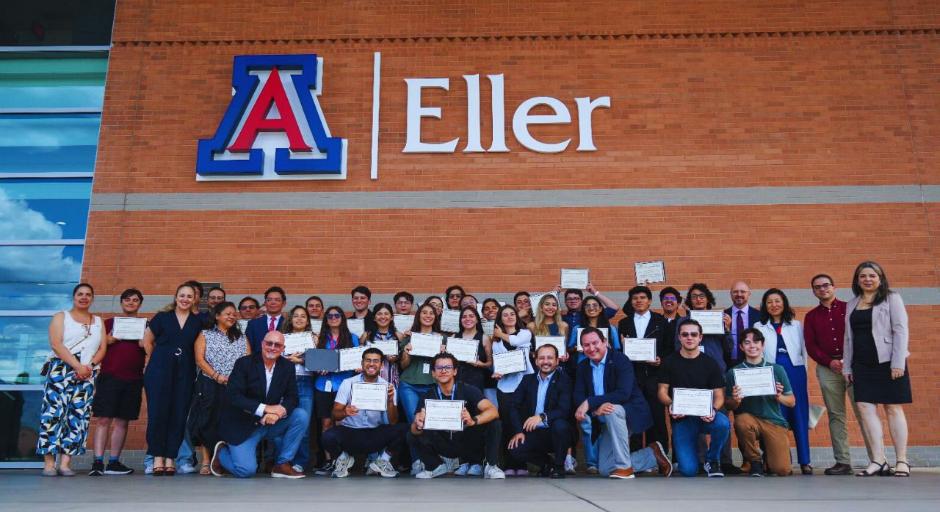
Chihuahua promueve educación sobre IA en Estados Unidos
El programa de Becas Internacionales Talento Chihuahua-COMEXUS concluyó oficialmente en la Universidad
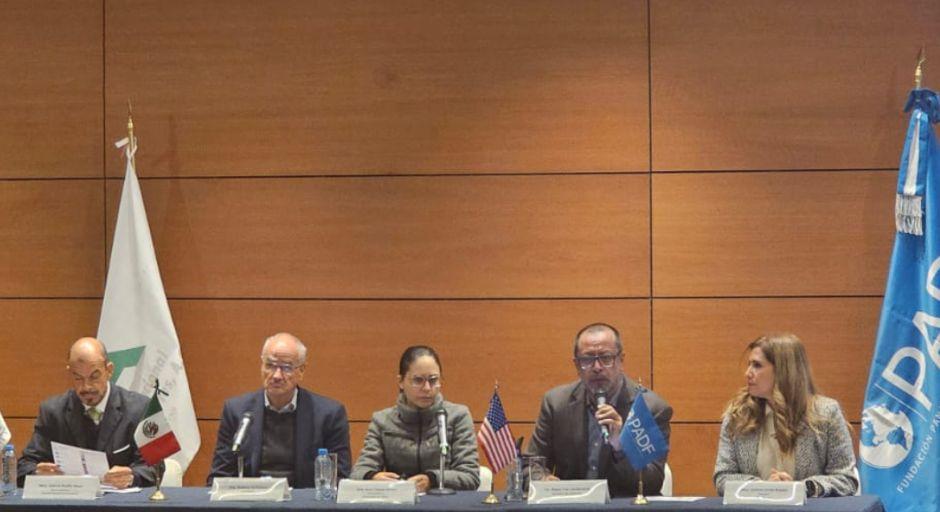
Crece en México producción de autopartes
La industria mexicana de autopartes registró en mayo de 2025 un incremento

Presentan columnas de señalización en planta
Con el objetivo de fortalecer la visibilidad de alertas dentro de entornos
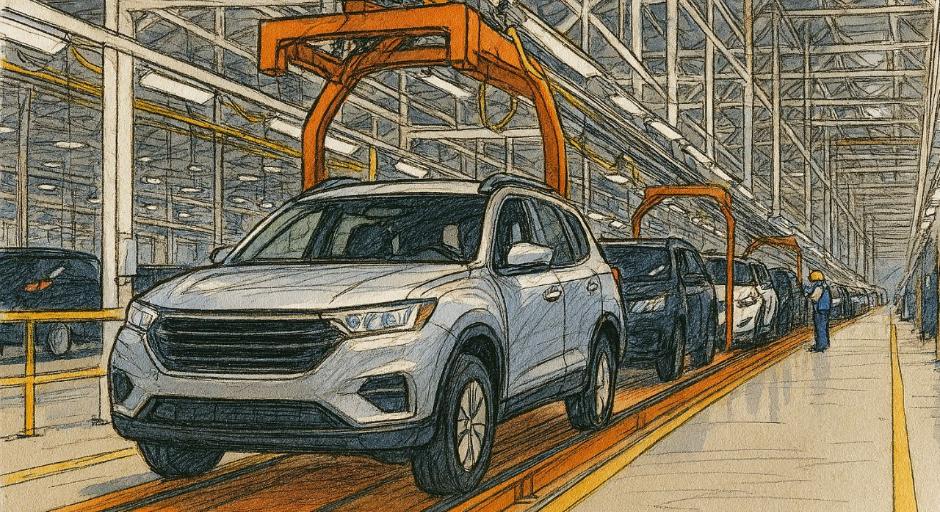
Aumenta producción de automóviles, cae consumo interno: INEGI
Información publicada por el Registro Administrativo de la Industria Automotriz de Vehículos
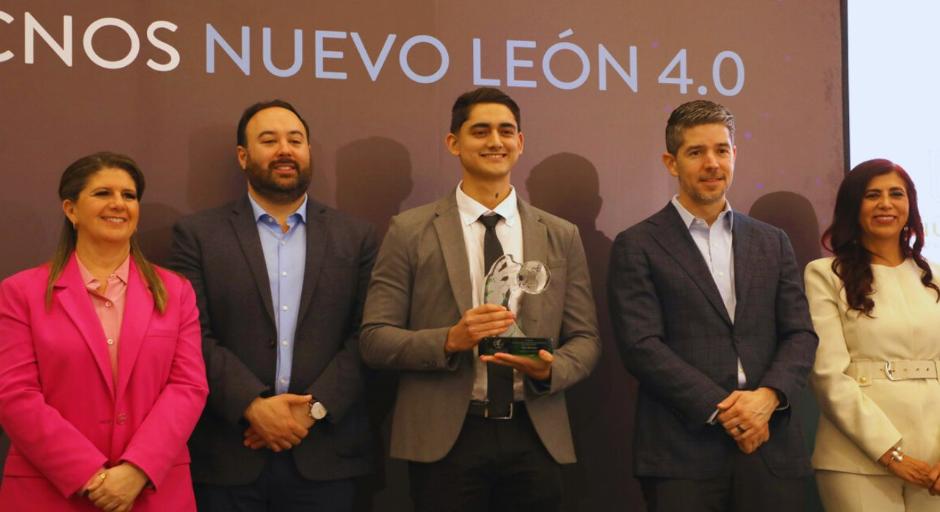
Finaliza Kia curso de formación juvenil STEM
El fabricante de automóviles, Kia México, graduó la segunda generación del programa
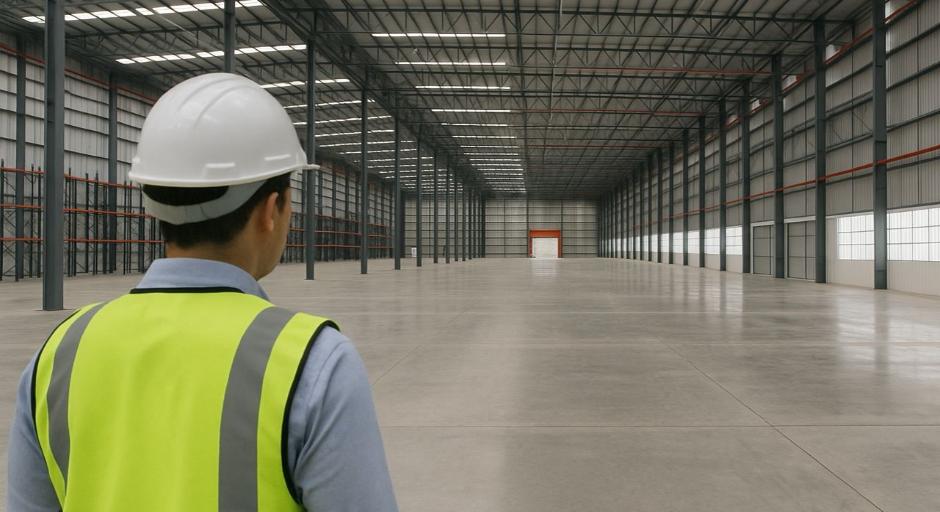
Aumenta demanda industrial en área metropolitana de CDMX
La actividad industrial en la Zona Metropolitana de la Ciudad de México